- Aproximadamente 300 toneladas al año
- Comparado con hornos de gas
Dingolfing, Alemania. BMW infoma que su Planta de Componentes Dingolfing 02.10, está operando con un nuevo horno eléctrico circular de forja, el cual, comparado con hornos de gas, disminuye la emisión de CO2 en cerca de 300 toneladas al año. En esta nueva tecnología, la compañía invirtió aproximadamente 7 millones de euros.
“El nuevo horno tiene una vida de servicio planeada de más de 40 años, por lo que es una pieza de equipo enfocada en el futuro, que establece el curso de nuestro trayecto hacia cero neto”, afirmó Marc Sielemann, Responsable de calidad y producción de sistemas de propulsión, chasis y frenos y Director de la Planta.
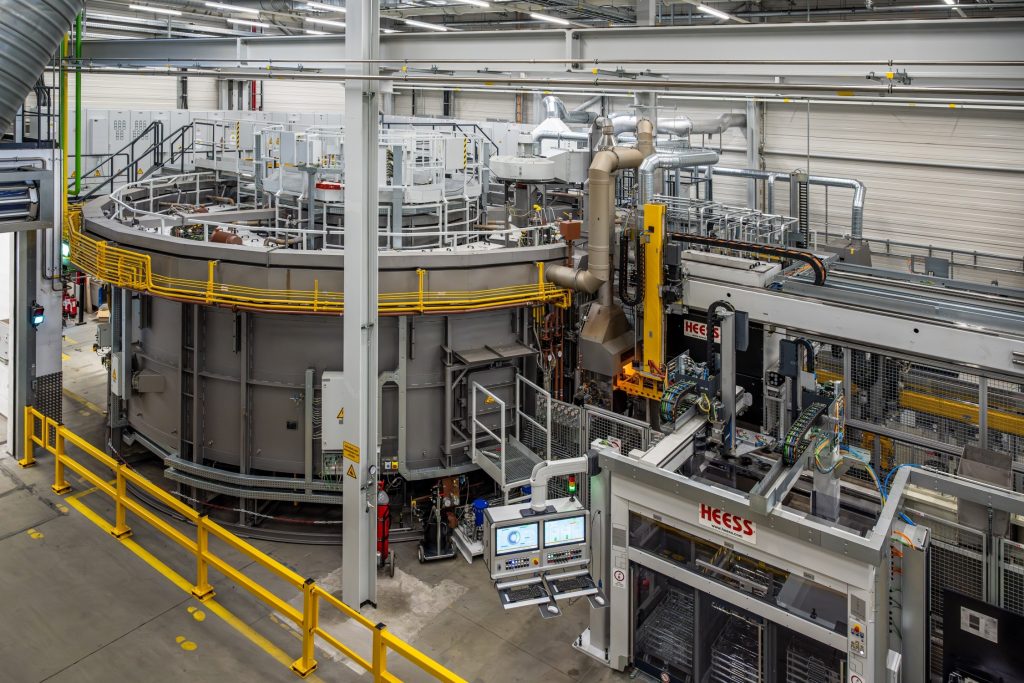
Para componentes e-drive.
En esta instalación producen chasises y componentes de tracción para autos BMW, MINI y Rolls-Royce. Para hacerlos más duraderos, las piezas se endurecen en hornos especiales. Además. conforme ha aumentado la oferta de autos eléctricos, se requiere cada vez más componentes, incluyendo los utilizados para las transmisiones eléctricas.
Utilizado para endurecer las ruedas dentadas de las transmisiones eléctricas, el innovador sistema tiene una capacidad de producción de aproximadamente 960,000 engranes rectos al año. Lo que tiene de especial es que, a diferencia de los dos hornos existentes, los cuales se alimentan con gas, esta nueva solución se alimenta con electricidad. En lugar de utilizar 33 llamas de gas en tubos con revestimiento de cerámica, como el modelo anterior, el nuevo horno utiliza la misma cantidad de elementos eléctricos para calentar hasta 900 grados centígrados.
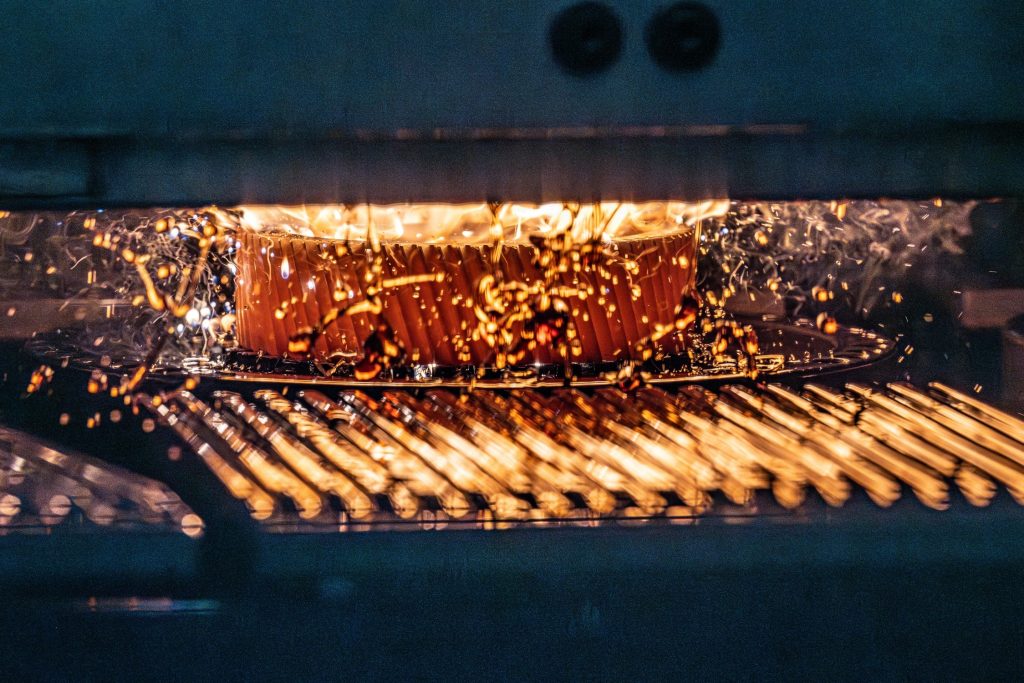
Menos emisiones de CO2
Esta nueva tecnología ahorra grandes cantidades de gases de efecto invernadero, los cuales son nocivos para el medio ambiente. Al funcionar con electricidad, el nuevo horno evita la emisión de aproximadamente 300 toneladas de CO2 al año.
“Los sistemas de energía para calentar de alto consumo energético como este nuevo horno eléctrico de forja circular apoyan la descarbonización de la generación de calor (un aspecto esencial de la protección climática). Generan calor con medios amigables con el medio ambiente y se pueden alimentar, entre otras cosas, con el excedente de energía de las energías renovables”, afirmó Sielemann. Por consiguiente, el nuevo horno con tecnología de energía para calentar no solo reduce el consumo de gas en la Planta de Dingolfing, sino que también apoya la integración de energías renovables en la red eléctrica. Éste es otro componente en la transformación de la BMW Group Planta Dingolfing hacia una fábrica BMW iFACTORY sustentable. “Para el futuro,” afirmó Sielemann, “estamos buscando convertir también los hornos de endurecimiento restantes a eléctricos”.